La ditta Sartorello è stata contattata dal responsabile di un’azienda cerealicola, in quanto gli operatori riscontravano un’elevata variabilità randomica della percentuale di umidità relativa del cereale in seguito al processo di essiccazione di una macchina datata.
Per risolvere il problema il settore informatico dell’azienda Sartorello, ha proceduto a customizzare il sistema di monitoraggio remoto (RMR), andando ad ampliare significativamente il controllo sul processo agendo anche in scrittura da remoto dei parametri di processo.
Motivo del problema
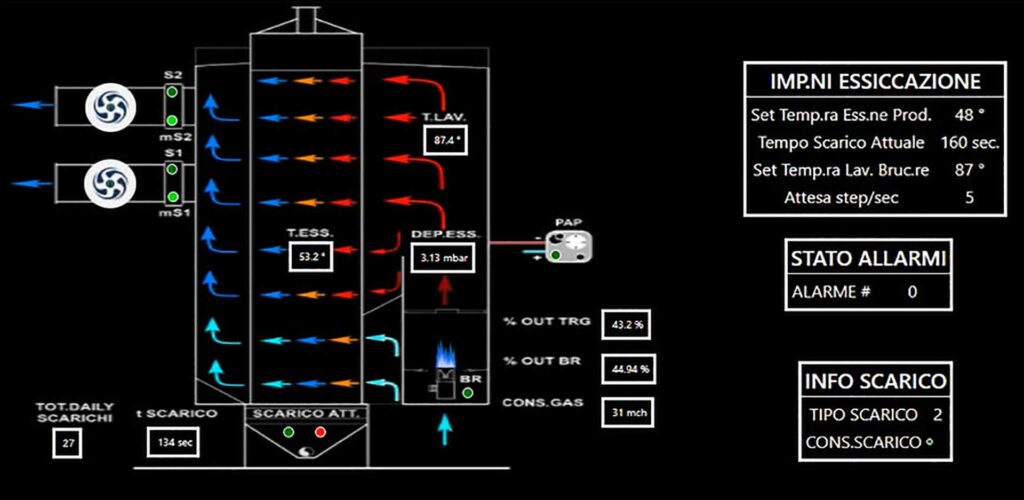
Il motivo del problema, vista l’età della macchina, è infatti dovuto al carente controllo che si ha del processo di essiccazione, causato dalla mancanza di un software di gestione dei tempi di scarico del prodotto e della temperatura di lavoro del bruciatore.
Il sistema installato, permette ora di avere piena visualizzazione di tutti i parametri, oltre la possibilità di poterli modificare. Il plc inoltre, adatta in automatico la temperatura di lavoro del bruciatore e i tempi di scarico dell’essiccatoio.
Supervisione e modifica
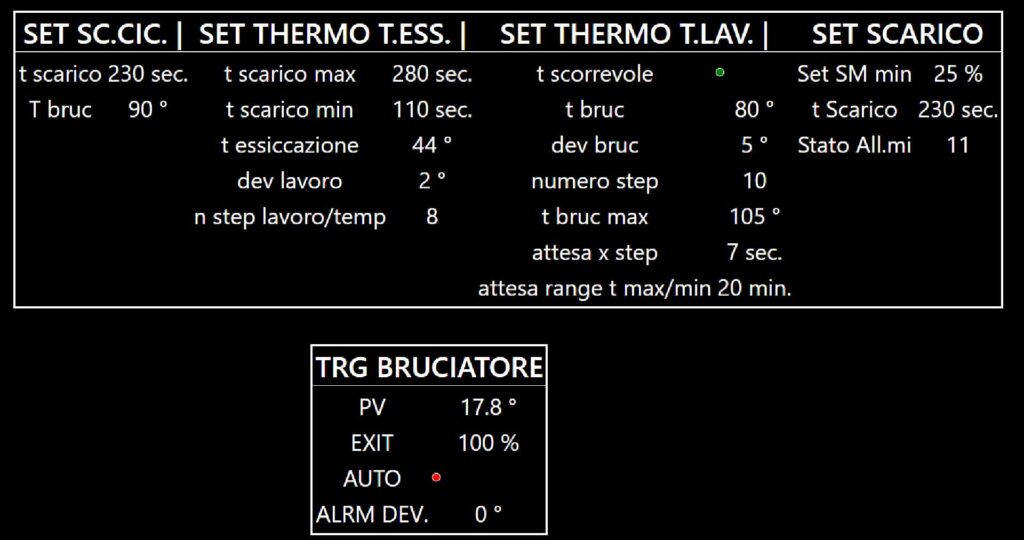
La supervisione e la modifica dei parametri può avvenire sia tramite la piattaforma web, sia in locale a mezzo dello schermo HMI presente sul quadro elettrico installato in cabina di controllo.
Per agevolare l’utilizzo ai dipendenti oramai abituati al vecchio sistema di controllo, si è provveduto ad effettuare una modifica mirata cercando di mantenere il più possibile gli elementi già presenti.
Per fare ciò si è provveduto inizialmente ad effettuare un sopralluogo durante il quale si è andati a:
- individuare la posizione migliore per poter posizionare un quadro ausiliario
- verificare e testare i sensori di temperatura presenti
- verificare dove installare i nuovi sensori necessari
- verificare la funzionalità modulante del bruciatore
- effettuare le foto relative agli apparecchi di comando con relativi collegamenti elettrici
Installazione finale
Una volta costruito il quadro elettrico ed effettuato il collaudo, si è proceduto all’installazione finale presso la sede del cliente.
A seguito del collaudo in loco e alla conseguente taratura delle variabili di gestione per un’ottimale essiccazione, è stato successivamente monitorato e registrato nei giorni successivi l’andamento grafico del processo con i seguenti i risultati:
come si evince dal grafico a lato, il 22 settembre 2021 è stato avviato l’impianto alle ore 7:00; in assenza di fermate alle ore 8:00 il processo era arrivato a regime, che come si può notare, fino alle ore 12:00 non si è mai discostato oltre il range aventi temperatura massima e minima rispettivamente di 52°C e 44°C, il che si traduce in una percentuale di umidità relativa oscillante tra il 12% e il 14.5%
una volta trascorse 5 ore dall’avvio*, il processo ha raggiunto la stabilità, il range si è notevolmente ridotto andando da un massimo di 47.5°C ad un minimo di 45°C, traducendosi in una percentuale di umidità relativa pari al 13/13.5%.
Da notare come la temperatura di lavoro del bruciatore sia cambiata nel tempo in maniera automatica gestita dal plc, al fine di mantenere costante la temperatura di essiccazione.
Obiettivi Raggiunti
- Automatizzazione del processo di essiccazione
- Azzeramento del rischio fermentazione in magazzino dovuti ad una errata essiccazione con tassi di umidità finale troppo elevati
- Controllo continuo dell’umidità di essiccazione
- Risparmio economico dovuto all’eliminazione di una eccessiva essiccazione, sia in termini di riduzione di peso del prodotto, sia in termini di minor combustibile utilizzato nel processo
- Notevole aumento dei dispositivi di sicurezza e monitoraggio della macchina
- Interazione con i parametri di processo da remoto, sia in lettura che in scrittura
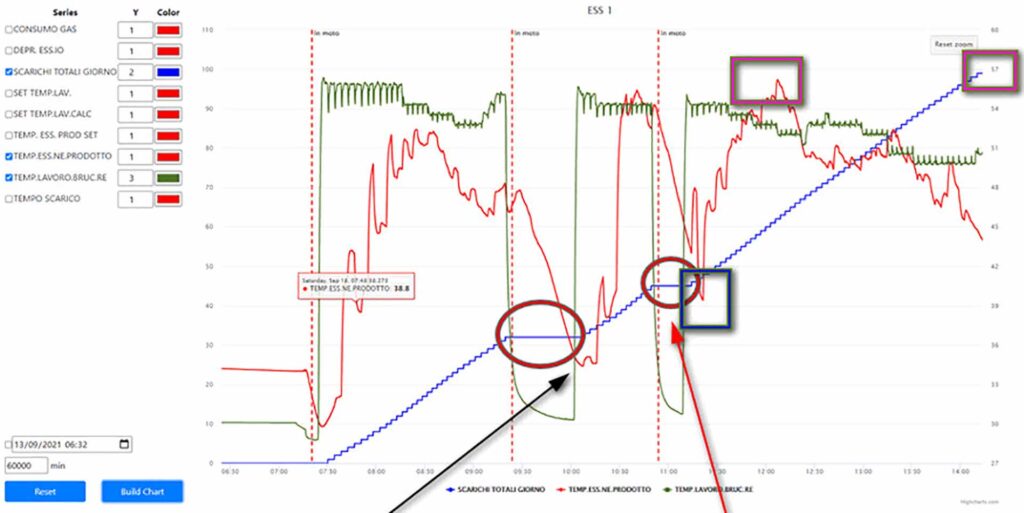
In seguito al raggiungimento degli obiettivi sopra riportati, si porta l’attenzione del lettore ad un ulteriore vantaggio comportato dall’istallazione del nuovo sistema RMR.
Si premette che il sito di essiccazione è una filiale di una spa; la quale viene gestita dai dipendenti mentre il titolare gestisce la sede centrale, per cui non è possibile avere la sua presenza costante in loco.
Il grafico adiacente rappresenta il processo d’essiccazione avvenuto il 3 ottobre, 4 giorni dopo l’avvio di RMR:
La linea a gradini di colore blu rappresenta il numero di scarichi totali di prodotto nell’arco della giornata.
Si può osservare come l’impianto sia stato messo in funzione come da programma alle ore 7:00, andando però incontro ad una fermata non programmata alle ore 9:20, durata ben 40 minuti; gli scarichi in seguito riprendono ad avere una cadenza regolare fino alle ore 10:50 dove avviene un’ulteriore pausa di 25 minuti.
Arrivati a questo punto, sorge spontaneamente nella mente del lettore un quesito, ovvero si domanda cosa può aver causato queste interruzioni nel processo produttivo.
I periodi d’arresto della produzione sono entrambi dovuti alla mancanza di prodotto nella buca di carico.
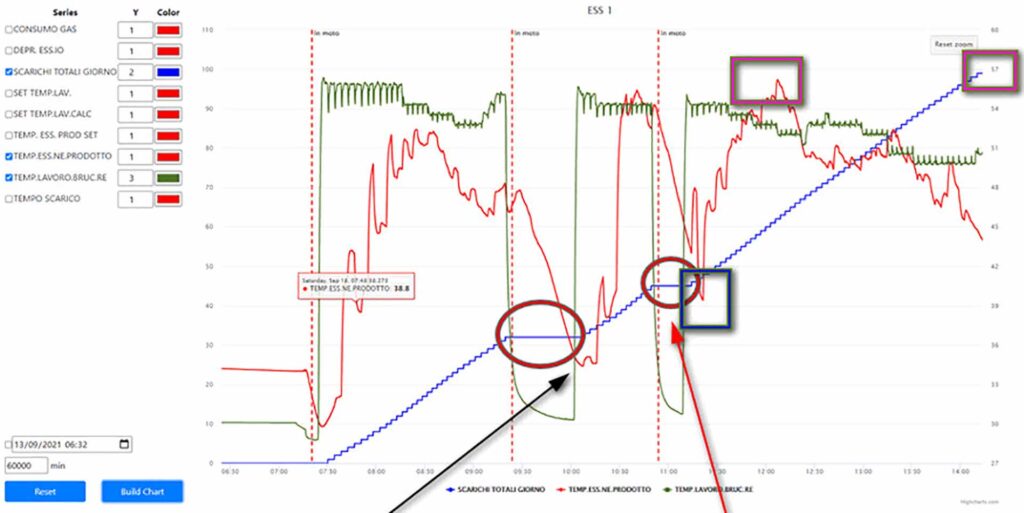
Come si può notare dal grafico, le due interruzioni non solo hanno provocato una perdita di produzione di oltre un’ora, ma la cosa peggiore è che all’interno il cereale ha subito alla fine due cicli di riscaldamento e raffreddamento, che hanno creato successivamente un’eccessiva essiccazione del prodotto fino a 57°C che, nel caso specifico di questa macchina, corrisponde a circa a 10% di umidità finale, per poi invece invertire fino a 39°C circa che corrisponde a 16%.
Lo sbalzo di umidità crea una perdita di peso del prodotto in caso di essiccazione eccessiva (umidità relativa del prodotto finale del 10%), e dall’altro lato, possibilità di avere all’interno della massa essiccata nello stoccaggio, zone in cui il prodotto fermenta e contamina quello adiacente nel caso di essicazione scarsa (umidità relativa del prodotto finale del 16%).
Il titolare dell’azienda, avendo a disposizione i dati soprariportati, ha provveduto ad ottimizzare le fasi di lavoro dell’azienda e dei suoi dipendenti, in maniera tale che il problema fosse risolto in maniera definitiva.
Nuovi Obiettivi Raggiunti
- Aumento della capacità produttiva del sito di essiccazione e ottimizzazione dei costi aziendali legati al personale dipendente
- Riduzione dei costi di energia elettrica per quintale di prodotto essiccato, in quanto, ogni volta che la macchina è in funzione, senza essiccare, consuma energia elettrica a vuoto
- Riduzione dei costi di combustibile per il fatto che ad ogni fermata la macchina ed il prodotto al suo interno si raffredda, e bisogna poi riscaldare tutta la massa nuovamente