La ditta Sartorello è stata contattata dal titolare di un caseificio, in quanto riscontrava:
- vari problemi di blocco improvviso del generatore, che si ripresentavano in maniera casuale
- danneggiamento pompa di carico acqua a seguito fattori esterni (es. cavitazione dovuta ad un eccessiva temperatura dell’acqua per surriscaldamento dovuto al ritorno condense)
- eccessiva alimentazione d’acqua generatore di vapore (es. per malfunzionamento dei livelli di carico)
- svuotamento completo caldaia, per malfunzionamento valvola defangatrice (es. per malfunzionamento timer di pausa/lavoro)
Non essendoci distinzione della causa di blocco, impossibilitava l’operatore ad indentificare e di conseguenza risolvere con immediatezza il problema.
Infine, è stato richiesto di poter variare in automatico il set point di lavoro nei periodi di pausa lavoro; essendo infatti un caseificio, la richiesta di vapore a 10 bar avviene soltanto dalle 5 alle 10 della mattina, e per le restanti 19 ore è sufficiente mantenere una pressione di 2 bar. Ai fini quindi di ottenere un risparmio energetico, la pressione viene abbassata.
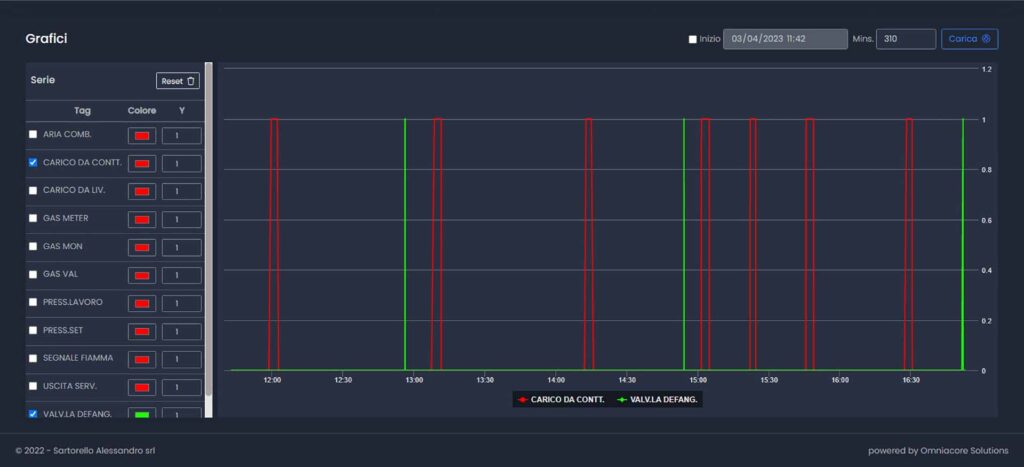
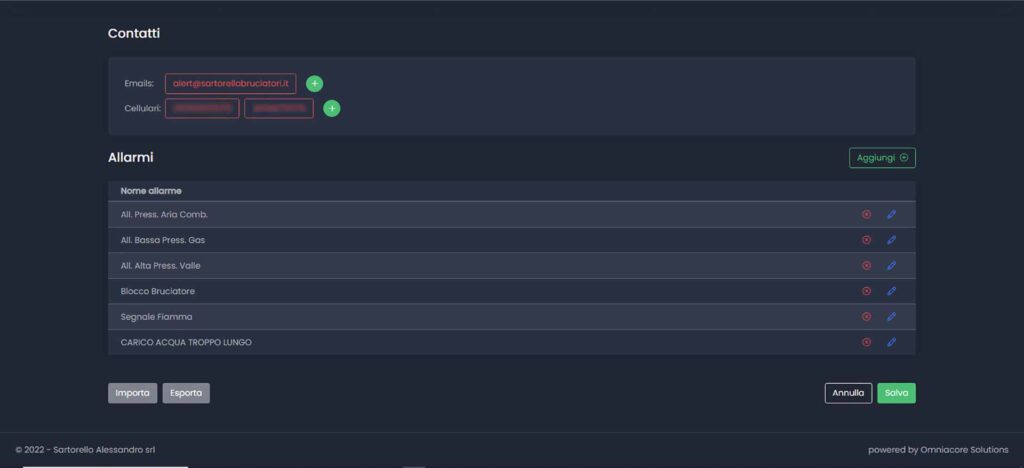
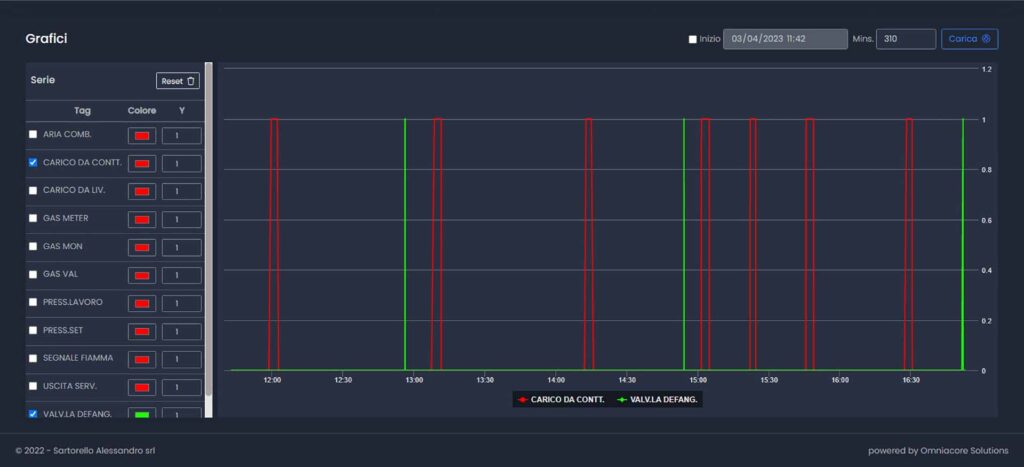
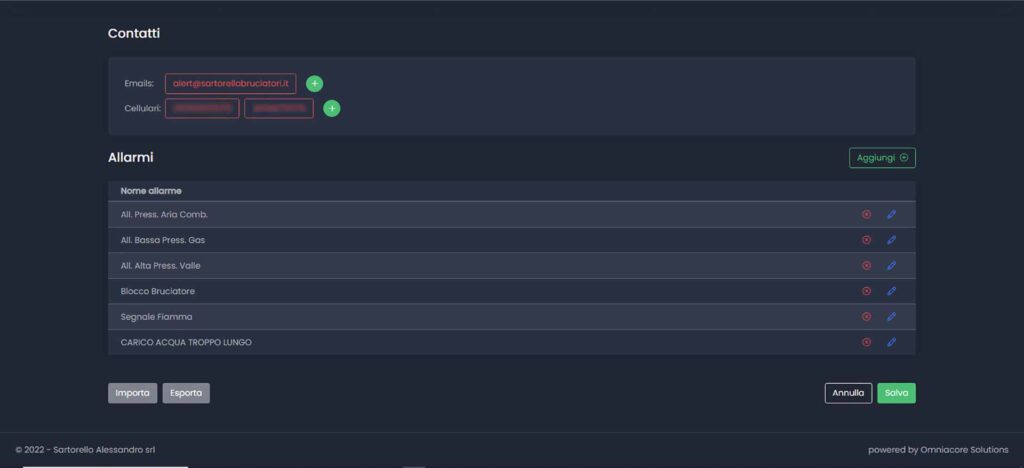
Di fronte alle suddette problematiche si è provveduto alla customizzazione e alla successiva installazione del nuovo sistema di controllo remoto RMR.
I problemi sono stati risolti grazie al monitoraggio continuo di tutti i singoli segnali relativi ai controlli di livello e dei pressostati di sicurezza e dei tempi di lavoro e pausa della pompa e della valvola defangatrice.
La sezione grafici e la pagina allarmi, permettono di identificare con assoluta precisione la causa del problema e di essere immediatamente avvisati in caso di anomalia, così evitando danni e soprattutto anti economici fermi impianto, come successo in data 03/07/2022 registrato dalla nostra pagina eventi.
Dalla piattaforma web è infatti consentito all’utente non solo di poter monitorare in tempo reale il valore della pressione relativa al generatore, ma di modificare il set point di lavoro e inoltre decidere i suoi relativi valori nell’arco della giornata, risolvendo in questo modo la problematica riferitaci, e raggiungendo così l’obiettivo di un risparmio economico, oltre che evitare l’inutile usura del generatore termico e dei suoi componenti dovuti al fatto di lavorare 24 h ad una pressione elevata non necessaria.
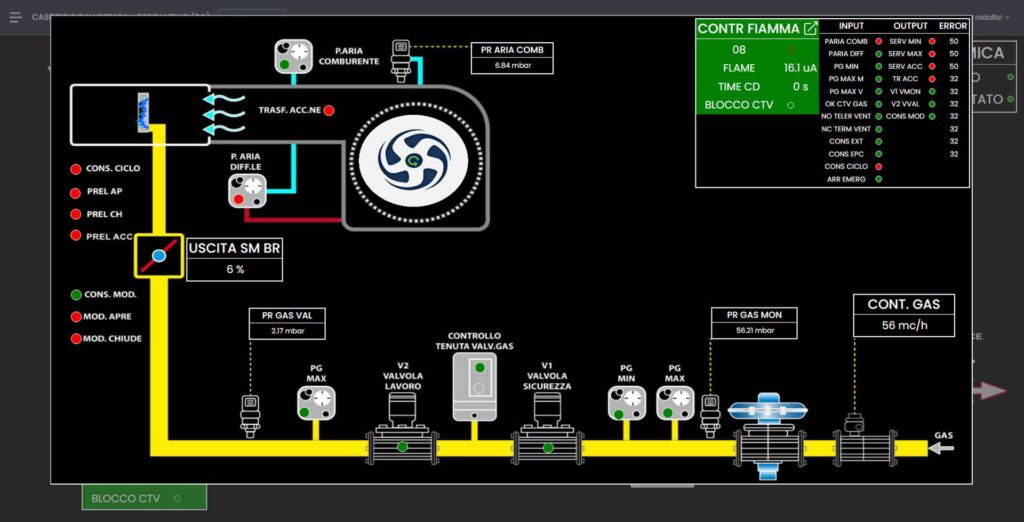
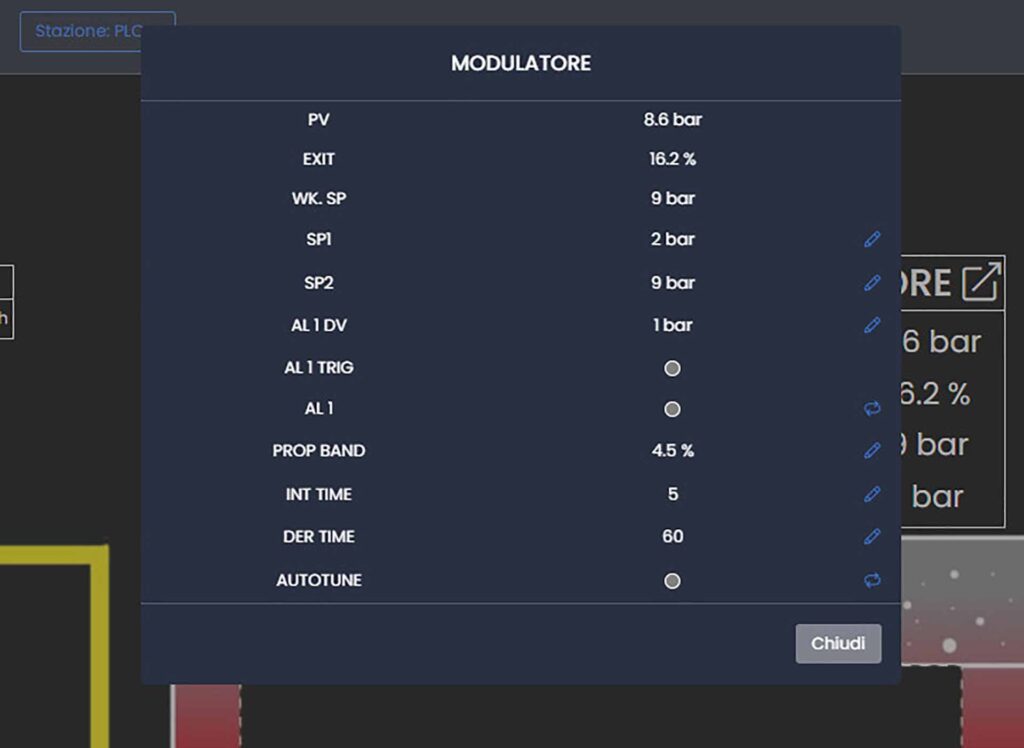
L’aggiunta di necessari componenti quali:
- trasduttori di pressione: sensori di pressione 4- 20 mA per il monitoraggio in tempo reale delle pressioni
- quantometro del gas: per il monitoraggio del consumo orario del combustibile
- potenziometro sul servomotore del gas per conoscere la percentuale di apertura
Permette accedendo alla piattaforma web di monitoraggio, di avere sotto controllo ogni singola variabile dell’impianto.
Questo ha non solo avuto come vantaggio la capacità di poter comprendere immediatamente i motivi di blocco dell’impianto stesso, diminuendo significativamente i tempi di arresto, ma permette inoltre alla servizio di assistenza tecnica di avere una visione in tempo reale del funzionamento del bruciatore. La supervisione della macchina termica tramite il sistema RMR da la possibilità di poter effettuare delle manutenzioni predittive, eliminando così i tempi di arresto improvvisi e la conseguente perdita economica che ne deriva.
Obiettivi raggiunti
- Riduzione dei costi energetici grazie alla variazione automatica del set point lavoro della pressione vapore generatore termico
- Minore usura del generatore termico e dei suoi componenti, con il vantaggio di un allungamento della durata nel tempo e minor rischio di rotture
- Azzeramento del rischio di danneggiamento pompa carico acqua a seguito fattori esterni
- Avviso immediato in caso di anomalia pompa carico acqua e valvola defangatrice, con conseguente forte riduzione possibilità di fermo impianto
- Manutenzione predittiva del generatore termico e del bruciatore